Why Does Dr Pepper Come in a Bottle? – Exploring the Benefits of Bottle Packaging for Dr Pepper
Dr Pepper is bottled to maintain its unique and carbonated taste.
Why Does Dr Pepper Come In A Bottle
Dr Pepper is often thought of as a deliciously refreshing carbonated beverage that comes in a unique bottle. But why? The truth is, Dr Pepper has been delivering its signature taste in bottles for over 130 years! This long-standing tradition of bottling Dr Pepper can be attributed to the beverage’s unique combination of 23 different flavors, which must be bottled to preserve their distinct taste. Furthermore, bottles provide maximum protection from air and light which further enhances the flavor experience. There’s no mistaking that famous bottle the thick glass walls keep Dr Pepper tasting fresh for a long time, ensuring you enjoy its signature taste with every sip!
History Of Dr Pepper Bottling
Dr Pepper has been around for over 150 years and, in that time, it has come to be associated with its iconic bottle design. The brand began in 1885 when pharmacist Charles Alderton created the drink in a drug store located in Waco, Texas. Initially, the beverage was sold as a fountain drink but as it grew in popularity, it was made available in bottles. The first Dr Pepper bottles were made from heavy glass and featured the distinctive red-and-white label that has become synonymous with the brand.
Benefits of Bottling Dr Pepper
Bottling Dr Pepper offers a number of advantages, including protection from external factors such as temperature and light that can affect the taste of the beverage. Additionally, bottling allows for easy transportation of the product from one location to another and makes it more accessible to consumers who may not have access to a fountain drink machine.
Association With Recognizable Bottle Design
The distinctive shape of the Dr Pepper bottle has become synonymous with the brand and is an important part of its identity. This recognizable design helps customers identify the product easily which can have a significant impact on brand recognition and sales. In addition, it helps distinguish pharmaceuticals from beverages on store shelves as they are often packaged in similar containers but with different designs or colors which can make them confusing to consumers.
Environmental Impact Of Dr Pepper Bottles
The environmental impact of using plastic bottles to package products such as Dr Pepper needs to be taken into consideration before making any decisions about production processes or packaging materials. While plastic bottles can be recyclable, they require energy consumption during production which is not ideal for sustainability purposes. Additionally, if plastic bottles are disposed of improperly they can cause significant damage to our environment by ending up in oceans or landfills where they take centuries to decompose.
Cost Effectiveness Of Dr Pepper Bottles
The cost effectiveness of using plastic bottles for packaging products like Dr Pepper needs to be taken into consideration when evaluating production costs versus profits. Factors such as shape and size will affect price points for both production and sale while material costs will also play an important role in determining final costings. Additionally, if recycling initiatives are implemented then this could help reduce overall costs associated with disposing of empty containers or packaging materials used during production processes.
Role of Others in Dr Pepper Bottling Process
The bottling process of Dr Pepper involves partnering with filling machines manufacturers and correlating with bottle suppliers as well. The process is tightly monitored to ensure the safety and quality of the end products. In order for the bottling process to be successful, it is essential for all parties involved to be in sync with one another. Filling machines manufacturers are responsible for producing the machinery needed to create bottles of Dr Pepper while bottle suppliers are essential in providing the containers needed to store the beverage. Without either of these parties, it would be impossible to package Dr Pepper into bottles that meet safety standards and consumer expectations.
Methods Used In Manufacturing Dr Pepper Bottles
Once all parts are accounted for, its time to begin manufacturing the actual bottles that will contain Dr Pepper. Two methods are commonly used when producing these bottles: shrink wrapping and blow molding. Shrink wrapping is a process where pre-made plastic films are heated up and then wrapped around a bottle or container shape before being cooled down so that they can take on a new form. This method is often used when creating plastic bottles as it is quick and efficient. On the other hand, blow molding is a method where molten plastic resin is pushed through an extrusion die before being forced into a mold cavity with air pressure. After this has been done, it can then take on its desired shape before being cooled down so that it can harden into place.
Safety Regulations for Manufacturing Dr Pepper Bottles
In order to ensure that each batch of manufactured bottles meets safety standards, there are a number of regulations set in place during the manufacturing process. Temperature and time regulations must be followed closely as this will affect both quality and safety of the final product. Health inspections protocols must also be observed as any contaminants found during this stage could result in health risks should they make their way into finished products.
Latest Technology In The Manufacturing Process
In recent times, advancements in technology have allowed for greater automation when manufacturing bottles for Dr Pepper which has significantly improved efficiency and productivity levels overall. Robotic arms have become commonplace on production lines due to their ability to perform precise tasks quickly without any human intervention required at all times while 3D printing technology has also been implemented in certain cases as well due to its ability to create complex shapes accurately at high speeds too. These technologies work together with other systems such as planning software which helps streamline processes even further by providing more accurate estimates on how long each stage will take while also ensuring that materials used during production stay within budget limits set by manufacturers too
FAQ & Answers
Q: What is the history of Dr Pepper bottling?
A: Dr Pepper began as a small business in Waco, Texas in 1885. The company grew and developed a new bottling process to keep up with demand. The modern Dr Pepper bottling process involves multiple steps, such as filtering the carbonated beverage, filling the bottles with the product, and labeling them before delivery.
Q: What are the benefits of bottling Dr Pepper?
A: Bottling Dr Pepper offers several advantages for both consumer and producer alike. Packaging the product in bottles helps to protect it from external factors such as heat or light which can affect the taste of the beverage. Bottles also make transportation and storage much easier for both consumers and businesses.
Q: How does bottle design impact brand recognition?
A: Since its inception, Dr Pepper has been associated with a recognizable bottle design that sets it apart from other soft drinks on the market. This distinct look has had a major impact on brand recognition; for many people, seeing this bottle shape is enough to identify the product as Dr Pepper. In addition, having an easily distinguishable bottle helps consumers quickly find their favorite soda among other products on store shelves.
Q: What is the environmental impact of using plastic bottles for Dr Pepper?
A: Using plastic bottles for packaging can have a negative effect on our environment if not managed properly. However, many of todays plastic materials are recyclable, which helps to reduce waste and energy consumption associated with producing new bottles each time. Additionally, some companies are beginning to use more environmentally-friendly materials such as sugarcane-based plastics when packaging their products.
Q: What role do others play in manufacturing Dr Pepper bottles?
A: In order to produce high-quality packages efficiently, there are many different entities involved in the process of manufacturing Dr Pepper bottles. Companies like filling machines manufacturers work closely with producers so that they can quickly and accurately fill each container with product; bottle suppliers also provide businesses with durable containers which can withstand wear-and-tear during transportation or storage; finally, certain safety regulations must be met so that consumers receive safe products every time they make a purchase.
In conclusion, the unique flavor of Dr Pepper was the primary reason for the decision to bottle it. The iconic bottle has become a symbol of the brand, and has been used in marketing campaigns to draw attention to the product. The shape and size of the bottle also make it easier to transport and store Dr Pepper, which is an important factor in its success.
Author Profile
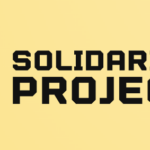
-
Solidarity Project was founded with a single aim in mind - to provide insights, information, and clarity on a wide range of topics spanning society, business, entertainment, and consumer goods. At its core, Solidarity Project is committed to promoting a culture of mutual understanding, informed decision-making, and intellectual curiosity.
We strive to offer readers an avenue to explore in-depth analysis, conduct thorough research, and seek answers to their burning questions. Whether you're searching for insights on societal trends, business practices, latest entertainment news, or product reviews, we've got you covered. Our commitment lies in providing you with reliable, comprehensive, and up-to-date information that's both transparent and easy to access.
Latest entries
- July 28, 2023Popular GamesLearn a New Language Easily With No Man’s Sky Practice Language
- July 28, 2023BlogAre You The Unique Person POF Is Looking For? Find Out Now!
- July 28, 2023BlogWhy Did ‘Fat Cats’ Rebrand and Change Their Name? – Exploring the Reasons Behind a Popular Name Change
- July 28, 2023BlogWhat is the Normal Range for an AF Correction 1 WRX?