How to Avoid Accruing Three Defects in the Trailing 120 Days
If three defects are accrued in the trailing 120 days, the account will be at risk of suspension.
If You Accrue Three Defects In The Trailing 120 Days
If You Accrue Three Defects In The Trailing 120 Days, it could have far-reaching consequences. It is a critical measurement that impacts the profitability of a corporation. Defects refer to any oversight, mistake, or incident that results in increased costs for the company. Companies often measure these defects over a period of 120 days to evaluate their current performance levels and identify areas for improvement. Accruing three defects means that your company is not meeting its benchmarks and needs to take corrective measures. By doing so, your business can improve its efficiency and cost-effectiveness, leading to greater profits down the line.
The Defects Problem in the Last 120 Days
Accruing three defects in the trailing 120 days can be a serious issue for any organization. Defects are defined as errors or discrepancies in data, process, or product that result in a negative impact on the customer or client experience. This can occur when a company fails to meet product standards, customer service expectations, or regulatory requirements. The impact of these defects can range from minor issues such as delayed shipment to major issues such as product recalls or costly fines.
Understanding the Gravity of Defects
It is important for companies to understand the severity of the defects they are producing. The seriousness of each defect should be evaluated and given an appropriate level of sanction. This will help ensure that corrective action is taken in a timely manner so issues can be addressed and resolved quickly and effectively. Companies should also track their defects to identify trends and discover root causes so they can make proactive changes to their processes and improve their overall quality assurance program.
Why You Should Monitor Your Defects
Monitoring your defects is essential for any organization looking to reduce risk and improve customer experience. Identifying issues early on will help mitigate them before they become more serious problems that require costly waivers or corrective action plans (CAPs). It is also important to acknowledge risk early on so that companies can prepare and create mitigating strategies before its too late.
Consequences of Too Many Defects
Accruing too many defects over a period of time can have dire consequences for any organization. If left unchecked, these problems could result in penalties and sanctions from regulatory bodies or costly fines from customers who are unhappy with your product or service. Mitigation strategies should be put into place to reduce the number of defective products produced and ensure that customers receive quality products and services at all times.
Identifying and Avoiding Common Traps
It is important for companies to be aware of common traps that could lead to accruing three defects in the trailing 120 days. Unforeseen regulatory requirements, unexpected repercussions, or even small mistakes such as incorrect labeling can all lead to costly errors down the line if not addressed properly. Companies should pay close attention to new regulations and industry standards so they can take proactive steps towards preventing these traps before its too late.
If You Accrue Three Defects In The Trailing 120 Days
Accruing three defects in the trailing 120 days can be a sign of trouble for any company. With the increased scrutiny on companies in today’s world, it is important to take proactive steps to prevent further issues. In this article, we will look at how to move forward after three defects, mitigating the risk of future defects, and regulations and responsibilities for compliance officers. We will also discuss when three defects are grounds for termination.
How To Move Forward After Three Defects
When you have accrued three defects in the trailing 120 days, it is important to evaluate the processes you already have in place. If your processes are inadequate, then you need to consider making changes. This means implementing better controls that can help prevent future issues from occurring and ensuring that all employees understand their roles and responsibilities when it comes to compliance. Additionally, if necessary, you should consider changing tactics or strategies if your current ones aren’t working as intended.
Mitigating The Risk Of Future Defects: A Proactive Approach
The best way to mitigate the risk of future defects is by being proactive. Managers should put reasonable controls in place that ensure compliance with industry standards and regulations. This could include things like having regular audits or reviews of processes and procedures, as well as setting up robust compliance measurements that detect any non-compliance before it can cause an issue. Additionally, having a documented oversight methodology can help ensure that all areas of the business are monitored properly and accurately.
Regulations And Responsibilities For Compliance Officers: Overview
Compliance officers need to understand their responsibilities when it comes to ensuring compliance with industry standards and regulations. This includes having a clear understanding of what is required by law and making sure that all relevant policies are followed correctly. Additionally, payment solutions should be put into place so that any potential issues are identified quickly and dealt with accordingly.
When Are Three Defects Grounds For Termination?
The answer to this question depends on the company’s policies and procedures regarding termination for non-compliance with industry standards or regulations. It is important for employees to know their rights as well as the scope of their employment when it comes to these matters so they know what could happen if they accrue three or more defects in the trailing 120 days. Furthermore, it is important for companies to learn from past instances so they can ensure similar issues do not arise again in the future.
FAQ & Answers
Q: What are the Defects Problem in the Last 120 Days?
A: Defects in the last 120 days refer to the occurrence of any irregularities while performing tasks, processes or operations in a given period of time. These can include errors in data entry, customer service issues, processing delays or incorrect product output. The impact of these defects can range from minor inconveniences to major losses.
Q: What is the Gravity of Defects?
A: The gravity of defects is defined by how serious they are and what level of sanction should be applied to them. Generally, defects are classified into four categories based on their severity ranging from minor (low) to critical (high). The level of action taken should be relative to the seriousness of the defect.
Q: Why Should I Monitor My Defects?
A: It is important to monitor your defects so that you can acknowledge and address risks early on and proactively reduce any potential waivers or exemptions that may occur when something goes wrong. By being aware of potential problems, you can take the necessary steps to mitigate their impact and ensure future compliance.
Q: What Are The Consequences Of Too Many Defects?
A: If too many defects occur within a given time frame, then it may result in penalties or sanctions being placed on your organization as well as possible additional mitigation strategies which may need to be implemented. In some cases this could also lead to termination depending on the number of defects and their severity.
Q: How Can I Move Forward After Three Defects?
A: After three defects have occurred it is important to evaluate all processes that are currently in place and make changes where necessary. Additionally, a proactive approach should be taken in order to mitigate any future risks with robust compliance measurements and reasonable controls for managers in place.
If you have accrued three or more defects in the trailing 120 days, it is important to address these issues as soon as possible. Doing so will help ensure that you stay in compliance with the applicable regulations and avoid any potential penalties or sanctions. It is also important to review your processes and procedures to identify the root causes of the defects and take corrective action to prevent similar issues from occurring in the future.
Author Profile
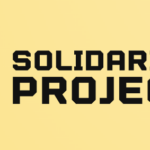
-
Solidarity Project was founded with a single aim in mind - to provide insights, information, and clarity on a wide range of topics spanning society, business, entertainment, and consumer goods. At its core, Solidarity Project is committed to promoting a culture of mutual understanding, informed decision-making, and intellectual curiosity.
We strive to offer readers an avenue to explore in-depth analysis, conduct thorough research, and seek answers to their burning questions. Whether you're searching for insights on societal trends, business practices, latest entertainment news, or product reviews, we've got you covered. Our commitment lies in providing you with reliable, comprehensive, and up-to-date information that's both transparent and easy to access.
Latest entries
- July 28, 2023Popular GamesLearn a New Language Easily With No Man’s Sky Practice Language
- July 28, 2023BlogAre You The Unique Person POF Is Looking For? Find Out Now!
- July 28, 2023BlogWhy Did ‘Fat Cats’ Rebrand and Change Their Name? – Exploring the Reasons Behind a Popular Name Change
- July 28, 2023BlogWhat is the Normal Range for an AF Correction 1 WRX?