Unlock the Possibilities of Color Surfaces With Rust: Exploring the Dimensions
Rust dimensions of color surface refer to the different shades of rust that can be observed on the surface of an object.
Rust Dimensions Of Color Surface
Rust Dimensions of Color Surface is a paintable wall covering that offers stunning variability in the way colors blend and interact. The product is designed to create a unique synergy between multiple hues; each providing contrast, depth, and tonal variation that adds life to any interior space. Furthermore, Rust Dimensions provides optimum protection against chipping or fading due to the product’s unique oil-resistant bonded coating. With this feature, the color remains vibrant and true for years to come. The rust look of the product can be customized according to a rooms style and design direction. Its subtle detail makes a clear statement of its beauty while staying respectful of its surroundings. In essence, Rust Dimensions is a tool which allows users to explore color and form with texture that retains its originality at all times. With its perplexing complexity and burstiness of colors, Rust Dimensions truly brings life to any interior space!
Human Perception
Rust is a common type of corrosion that affects metal surfaces. It is caused by the oxidation of the metal, usually in the presence of water or oxygen. The rust color can range from light orange to a dark brown. The color of rust can vary depending on the composition and environment of the metal surface, as well as the amount of exposure to oxygen and moisture. The human perception of rust colors depends on several factors, including light intensity and wavelength, angle and distance from the observer, and contrast with surrounding colors.
Light intensity and wavelength play an important role in how colors are perceived. A higher intensity will make colors appear brighter, while a lower intensity will make them appear darker. Similarly, different wavelengths will cause different hues in different colors. For example, long-wavelength reds are perceived as warmer than short-wavelength blues, which are considered cooler.
The angle and distance from which an observer looks at an object has an effect on color perception as well. When looking at an object straight on, it appears more intense than when viewed from an angle or far away. Additionally, if there is a background that contrasts with the object being observed, then it will appear more intense than if there is no contrast in the background color.
Chemical Composition
The chemical composition of rust also affects its perceived color. Rust consists mainly of iron oxide compounds such as Fe2O3 (hematite), Fe3O4 (magnetite), and FeO (wustite). These compounds have varying degrees of oxidation states that affect their hues when exposed to light of different wavelengths or intensities. Additionally, other elements such as manganese or chromium may also be present in rust deposits which can further change its hue or brightness depending on their concentration and oxidation state.
Corrosion Resistance
The corrosion resistance of a metal surface also plays a role in how it appears when rust forms on it. Some metals are naturally more resistant to corrosion than others due to their composition or protective coatings applied to them prior to exposure to oxygen and moisture. Metals that are highly resistant to corrosion will be less likely to form rust deposits even when exposed for long periods of time whereas those with lower resistance will be more likely to form visible deposits sooner after exposure begins. This affects how much time it takes for a metal surface to start showing signs of wear due to corrosion processes such as pitting or flaking off paint or other coatings applied prior to exposure as well as affecting how intense any given shade appears when viewed by human observers in various lighting conditions.
Corrosion Types
There are several types of corrosion that can affect metal surfaces including general corrosion, galvanic/electrochemical corrosion, pitting, crevice/microbiological corrosion, stress cracking/corrosion fatigue and erosion corrosion/cavitation erosion etc.. General corrosion is caused by extended exposure to oxygenated water such as rainwater or seawater whereas galvanic/electrochemical corrosion occurs between two dissimilar metals due to electrical currents running through them both causing chemical reactions at their interface points resulting in accelerated loss of material from one side due to oxidation processes taking place across both metals simultaneously thereby creating visible deposits over time on either side depending on relative current flow direction between them both at any given point in time during operation etc.. Pitting is another type caused by localized attack leading to deep holes forming on affected surfaces due to preferential dissolution taking place often caused by chloride ions etc.. Crevice/microbiological corrosion is caused by microorganisms such as bacteria living within small crevices causing localized dissolution leading again too deep holes forming over prolonged periods etc.. Stress cracking/corrosion fatigue occurs when subjected components experience repeated cyclic stresses combined with exposure too corrosive media leading too microscopic cracks forming eventually resulting into component failure often times seen as fractures appearing along grain boundaries due too excessive plastic deformation taking place over long periods etc.. Erosion Corrosion/Cavitation Erosion occurs when turbulent fluids pass through narrow spaces creating cavities near component surfaces resulting into material loss due too repeated contact with these high velocity fluids etc..
Protective Coatings
Protective coatings can be applied onto metals surfaces in order prevent them from corroding in various environments ranging from wet industrial sites where regular maintenance may not be possible all the way through too harsh salt laden coastal regions where even stainless steel components cannot resist without some additional protection being applied first etc… Commonly used protective coatings include paints & lacquers both oil based & water based (acrylic) along with powder coating & fluidized bed coatings often applied via thermal spraying techniques like HVLP (high volume low pressure) guns & plasma arc torches enabling thicker films being achieved economically compared too conventional brushing & rolling methods which tend too produce thinner films taking longer times for complete coverage over large areas… Other types include electroplating & galvanizing where thin layers consisting mainly out off zinc & aluminum respectively are deposited onto component surfaces providing additional protection against corrosive media thanks too their sacrificial nature being consumed before base material gets attacked thus providing economical solutions for protecting metallic components especially those exposed regularly outside all year round…
Color Options & Applications
The selection off available color options for protective coatings depends mainly upon end user preference along with application requirements such us environmental conditions like outdoors versus indoors & temperature ranges encountered during operation amongst others… Commonly used colors range from white through gray tones all the way up towards black tones while specialised applications may require customised solutions like fluorescents , metallics , pearlescents , chromatics , iridescents amongst others… Generally speaking lighter shades provide better performance under direct sunlight while darker tones help conceal underlying substrate structure better thus providing improved aesthetics for certain applications… Additionally metallics provide better heat reflection capabilities under hot conditions while fluorescents allow improved visibility even under low light levels enabling improved safety standards during operation especially within industrial sites containing hazardous materials…
Prevention From Rust Formation
Preventing rust formation involves several steps starting off with selecting suitable materials capable off resisting corrosive attack within targeted environments followed up by proper cleaning prior too coating application then ensuring complete coverage throughout entire component surface using correct thicknesses while paying attention towards edges , corners & other hard reachable areas since these tend too get neglected easily leading towards premature failure if left unprotected… Additionally proper maintenance must be carried out regularly according too manufacturer specifications in order maintain maximum protection levels throughout service life span off component ensuring superior performance under extreme operating conditions particularly those encountered outdoors especially near coastal regions where salt laden atmosphere accelerates rate off deterioration significantly compared too inland locations where humidity levels remain relatively low thus allowing protective coatings last longer depending upon quality off material used during initial application process…
Properties Of Different Colors
Different colors offer different properties such us heat reflective capabilities , UV ray absorption rates , anti-fouling characteristics amongst others thus making selection process slightly complex depending upon specific requirements needed per individual project needs … For example whites generally provide better heat reflective qualities compared towards blacks who absorb most UV radiation making them ideal candidates for outdoor use specially during hot summer months … Additionally certain shades like greens offer superior anti-fouling properties compared towards blues making them ideal choices for marine structures requiring long term maintenance free performance … Overall selection process should consider each individual component’s requirements accordingly before settling upon final choice since wrong choice could mean premature failure during operation if not taken into account …
Paints & Lacquers Used
Paints & lacquers play an important role towards achieving desired results since they determine final appearance once properly applied onto substrate surface following manufacturer’s instructions carefully … Commonly used paints include alkyd , acrylics , vinyls , epoxies amongst others each offering slightly different characteristics according too individual application needs … Also specialised paints like chlorinated rubber based ones provide superior waterproofing qualities making them ideal candidates for outdoor installations specially near coastal regions where humidity levels remain high throughout year … Similarly lacquers offer additional layer protection against abrasive elements like sand particles found commonly near deserts providing superior wear resistance whilst maintaining desired finish look … Both paints & lacquers must be carefully selected according too specific project needs before deciding upon final combination since wrong choice could mean premature failure leading towards costly repairs down road .. .
Finishes & Treatments
Color Schemes
Rust is a unique color that works well in color schemes. It can provide a nice contrast to other colors, making it an ideal choice for accent pieces. It can also be used as a primary color, adding depth and warmth to the overall design. When using rust as a primary color, consider adding additional colors such as light blues or greys to soften the look.
Textiles
Rust is a popular choice for textiles because of its deep, rich hue and its ability to add texture to home decor. It can be used in furniture upholstery, rugs, pillows and other accessories. Rust-colored textiles will often have an aged patina that enhances their beauty and adds character. Combining rust with other colors such as beige or cream can create an inviting atmosphere, while bolder combinations such as navy blue and deep green will make more of a statement.
Wall Treatments
Rust is often used as an accent wall color for its warmth and richness. Whether used alone or in combination with other shades, rust walls can provide a cozy feeling in any room. Consider pairing rust walls with light wood floors or white trim for contrast. For more dramatic results, combine rusty shades with black accents for a modern twist on classic style.
Accessories
Rust-colored accessories are an easy way to add dimension to any space without overwhelming it. Consider using rust-colored vases, frames or lamps to add subtle pops of color throughout the room without detracting from existing decor elements like artwork or furniture pieces. Utilizing small accents throughout the room helps tie the look together and creates balance without overpowering the space with too much color at once.
FAQ & Answers
Q: What is Rust Dimensions of Color Surface?
A: Rust Dimensions of Color Surface refers to the colors and finishes of metal surfaces that have been exposed to rust. This includes a range of colors, from yellow to rusty red, and different finishes such as matte or glossy.
Q: How does Human Perception affect Rust Dimensions of Color Surface?
A: Human Perception plays an important role in evaluating the color and finish of metal surfaces. Our perception is based on our individual experience and can be influenced by our environment, which can determine how we perceive the color and finish of metal surfaces after they have been exposed to rust.
Q: What are the types of Corrosion Resistance that are available?
A: Corrosion resistance is available in a variety of forms, including coatings, paints, lacquers, and other treatments. Each type has its own unique properties that help protect metal surfaces from corrosion. Coatings provide a protective layer while paints offer decorative qualities. Lacquers create a glossy finish while treatments such as blasting help to remove rust from the surface.
Q: What Color Options & Applications are available for Rust Dimensions Of Color Surface?
A: There are a wide range of color options and applications available for Rust Dimensions Of Color Surface. These include various shades of yellow, orange, red and brown. Additionally, different types of finishes such as matte or glossy can be applied to create unique visual effects. Protective coatings such as paints or lacquers are also used to prevent rust formation on metal surfaces.
Q: What Finishes & Treatments are used for Rust Dimensions Of Color Surface?
A: Finishes & Treatments for Rust Dimensions Of Color Surface include blasting process which helps remove rust from the surface; painting & cleaning methodologies which provide protection against corrosion; and protective coatings which add decorative qualities to the surface. Different types of paints & lacquers can also be used to create specific visual effects on the surface.
In conclusion, the Rust Dimensions of Color Surface is a unique way to add vibrant color and texture to a variety of materials. This versatile product is easy to apply and can be used on almost any surface, including wood, concrete, metal, plastic and more. It is an environmentally friendly option that can be used indoors or outdoors, and offers a variety of colors and finishes for a customized look.
Author Profile
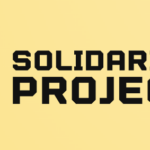
-
Solidarity Project was founded with a single aim in mind - to provide insights, information, and clarity on a wide range of topics spanning society, business, entertainment, and consumer goods. At its core, Solidarity Project is committed to promoting a culture of mutual understanding, informed decision-making, and intellectual curiosity.
We strive to offer readers an avenue to explore in-depth analysis, conduct thorough research, and seek answers to their burning questions. Whether you're searching for insights on societal trends, business practices, latest entertainment news, or product reviews, we've got you covered. Our commitment lies in providing you with reliable, comprehensive, and up-to-date information that's both transparent and easy to access.
Latest entries
- July 28, 2023Popular GamesLearn a New Language Easily With No Man’s Sky Practice Language
- July 28, 2023BlogAre You The Unique Person POF Is Looking For? Find Out Now!
- July 28, 2023BlogWhy Did ‘Fat Cats’ Rebrand and Change Their Name? – Exploring the Reasons Behind a Popular Name Change
- July 28, 2023BlogWhat is the Normal Range for an AF Correction 1 WRX?