How to Ensure Quality Control When Working with Vendors: A Guide for Businesses
Unfortunately, the vendors’ quality control did not meet expectations.
Unfortunately The Vendors Quality Control
Unfortunately, the Vendors Quality Control (VQC) can be an overlooked area when it comes to customer satisfaction. The VQC process involves ensuring that all products supplied to customers meet their quality standards. This is the responsibility of the vendor as well as the customer to ensure that quality products are delivered and received. In order to achieve this, vendors must have a proper quality control system in place that meets all demanded criteria. This includes inspecting each step of product development, from receiving raw materials to shipping finished products. With reliable and consistent checks along the way, vendors can guarantee customers get what they paid for without problems or delays. Furthermore, an effective VQC system helps vendors provide fast resolution and rectification in case any issues arise during or after delivery. By neglecting corresponding measures, customers may not only face delayed processing times but also put their trust into a failing business since a clear sign of reliability is missing.
Ensuring Vendors Quality Control
It is essential to ensure that vendors are meeting quality standards in order to maintain customer satisfaction, reduce costs, and ensure the safety of products. Regular inspections should be conducted to ensure that all quality standards are met. During these inspections, data should be collected to track any potential issues that may arise. This data can then be used to identify patterns and potential areas of improvement. Additionally, it is important to have processes in place that allow for quick corrective action when needed.
Compromising Quality Issues
It is inevitable that there will be some quality issues from time to time. It is important to have an overview of all complaints and what caused them in order to identify any root causes and take corrective action accordingly. This includes looking at both internal and external factors such as processes, suppliers, materials used, etc., in order to identify the issue and take steps towards resolving it.
Optimizing Quality Standards
In order to optimize quality standards, it is important to have policies and procedures in place that clearly define requirements for vendors as well as any acceptable ranges or parameters for different components or materials used. Training employees on these policies and procedures can help ensure they are followed correctly. Additionally, using data collected from previous inspection results can help identify areas for improvement or adjustment of policy parameters if needed.
Implementing Continuous Improvement Strategies
Continuous improvement strategies should always be implemented in order to ensure vendors are meeting quality standards over time. This can include monitoring performance indicators such as customer satisfaction levels or production throughput rates, as well as analyzing key performance metrics such as defect rates or lead times. By doing this regularly, trends can easily be identified which can then be addressed before they become a larger problem.
Lack of Accountability for Quality Defects
When there is a lack of accountability for quality defects it can lead to increased costs and customer dissatisfaction. In order to rectify this situation it is important to create customer-centric requirements which specify what the customer expects from each product or service provided by the vendor. Additionally, having standard review processes in place that involve multiple stakeholders allows for timely feedback on any potential issues so they can be addressed quickly and efficiently before becoming a larger problem down the line.
Unfortunately The Vendors Quality Control
Todays market is highly competitive, and its important for vendors to maintain quality control over their products and services. Unfortunately, many vendors fall short when it comes to properly monitoring and managing quality assurance standards. As such, customers receive lower quality products that are not up to standard. To ensure that vendors are providing quality services and products, there are several steps they can take to ensure customers receive the best possible experience.
Educating End Users on Quality Assurance Policies
One of the most important steps a vendor can take to ensure their services and products meet the highest standards is by educating end users on quality assurance policies. Product certification programs help end users understand the scope of a vendor’s product or service and how it meets their needs. User manuals and guides provide detailed instructions on how to use a product or service correctly so customers know exactly what they should expect from their purchases. By educating customers on quality assurance policies, vendors can ensure that they deliver products and services of the highest standards to meet customer expectations.
Maximizing Benefits of Quality Enhancement Programs
Quality enhancement programs are designed to help vendors improve the overall quality of their products and services. By engaging in client engagement practices, vendors can better understand customer needs and create more tailored solutions that meet those needs more effectively. Staff training programs also help vendors identify areas for improvement in terms of product or service delivery so that they can develop new processes or procedures for improvement. By taking advantage of these quality enhancement programs, vendors can make sure they are providing customers with the highest level of service possible.
Developing Effective Documentation Practices
Documentation plays an important role in helping vendors maintain consistent standards across all aspects of their operations. Updating document templates regularly ensures that all documents accurately reflect current processes or procedures as well as any changes made over time. Additionally, version control practices should be employed which track revisions made to documents so that previous versions can be easily retrieved if needed. By developing effective documentation practices, vendors can make sure all documents are up-to-date and properly managed so they accurately represent current operations at all times.
FAQ & Answers
Q: What is Quality Control?
A: Quality Control (QC) is a process used to ensure that a product or service meets the requirements of the customer or client. It involves testing and inspecting products during the production process to identify any potential areas of improvement.
Q: What are the steps to ensuring vendors quality control?
A: The steps for ensuring vendors quality control include regular inspections, data collection, identifying root causes of quality issues, creating customer-centric requirements, standard review processes, product certification programs, user manuals and guides, client engagement practices, staff training programs, updating document templates and version control practices.
Q: What are the benefits of quality enhancement programs?
A: Quality enhancement programs can help maximize benefits by increasing customer satisfaction through improved product quality. Additionally, these programs can result in cost savings due to fewer returns and warranty claims. Furthermore, they can help increase employee productivity by providing them with enhanced tools and resources for completing tasks more efficiently.
Q: How do you create accountability for quality defects?
A: Accountability for quality defects can be created by implementing new policies and procedures around quality assurance as well as providing regular training to employees on these policies. Additionally, creating customer-centric requirements and establishing standard review processes can help ensure that all products meet the necessary quality standards before being released to the public.
Q: How do you educate end users on quality assurance policies?
A: End users should be educated on quality assurance policies through product certification programs and user manuals/guides that contain information about how to properly use the product and its features. Additionally, staff training programs should be implemented so that employees have an understanding of how to efficiently use their tools and resources when addressing customer needs related to product quality.
In conclusion, The Vendors Quality Control is an important factor to consider when evaluating the success of a business. It is essential to have systems and processes in place that will ensure the quality of the products or services provided. Unfortunately, if these processes are not adequately implemented, it can result in significant losses for companies and customers alike. Therefore, it is important for vendors to continually evaluate and improve their quality control measures in order to ensure the best possible outcomes.
Author Profile
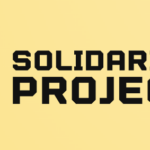
-
Solidarity Project was founded with a single aim in mind - to provide insights, information, and clarity on a wide range of topics spanning society, business, entertainment, and consumer goods. At its core, Solidarity Project is committed to promoting a culture of mutual understanding, informed decision-making, and intellectual curiosity.
We strive to offer readers an avenue to explore in-depth analysis, conduct thorough research, and seek answers to their burning questions. Whether you're searching for insights on societal trends, business practices, latest entertainment news, or product reviews, we've got you covered. Our commitment lies in providing you with reliable, comprehensive, and up-to-date information that's both transparent and easy to access.
Latest entries
- July 28, 2023Popular GamesLearn a New Language Easily With No Man’s Sky Practice Language
- July 28, 2023BlogAre You The Unique Person POF Is Looking For? Find Out Now!
- July 28, 2023BlogWhy Did ‘Fat Cats’ Rebrand and Change Their Name? – Exploring the Reasons Behind a Popular Name Change
- July 28, 2023BlogWhat is the Normal Range for an AF Correction 1 WRX?