Industrial Mixer Cleaning Leads to Tragic Loss of Life
A worker has tragically passed away while cleaning an industrial mixer.
Worker Killed While Cleaning Industrial Mixer
A tragedy occurred at an industrial business recently. A worker was killed while cleaning an industrial mixer. The circumstances behind the accident are currently under investigation, but it appears that the worker became trapped in the machinery while performing standard maintenance. The death has stunned and saddened the small community, which had grown accustomed to a safe work environment.
Safety protocols were in place to protect workers, including proper training and safety checklists. Technology such as shut-off switches and other automated systems were in place to ensure that any potential risks of using such machinery were minimized. It is unknown why the fatal accident occurred, and an investigation is being conducted to determine exactly what caused it.
The impact of this tragedy should not be underestimated; not only did a life tragically end, but its aftermath has repercussions on the whole community. As employers, we must strive for utmost safety in all of our daily operations in order to protect our workers and prevent further tragedies from happening again.
Industrial Accidents: The Danger of Working Hazardous Environments
Every day, workers in industrial settings are exposed to a variety of risks that could potentially harm them. From machine malfunctions to hazardous materials, there is always the possibility of an accident occurring and resulting in injury or even death. Unfortunately, this is exactly what happened when a worker was killed while cleaning an industrial mixer at a manufacturing plant. In such cases, it is important to understand the dangers associated with working in hazardous environments and take proper precautions to protect workers from harm.
The most common dangers associated with industrial accidents involve contact with hazardous materials or equipment. This includes exposure to chemicals, electricity, machinery, and heavy objects that can cause physical injury or illness. Additionally, there may be risks related to fire hazards or explosions due to outdated equipment or improper safety protocols. All of these risks must be addressed by employers in order to provide a safe workplace for their employees.
Worker Safety Measures
To help protect workers from potential hazards, employers should implement safety measures such as providing appropriate protective gear and conducting regular safety training sessions for their staff. It is also important that employers have designated areas where hazardous materials are stored and handled properly according to industry regulations. Additionally, employers should regularly inspect all machinery and equipment in order to identify any signs of wear or malfunction that could potentially lead to an accident. Finally, employers should have an emergency response plan in place so they can quickly respond if an accident does occur.
Cleaning Mixers: Maintenance Requirements
The unfortunate incident involving the worker killed while cleaning an industrial mixer highlights the need for proper maintenance and safety protocols when it comes to operating these types of machines. Industrial mixers require frequent cleaning and maintenance in order to ensure their proper functioning and reduce the risk of accidents occurring due to malfunctioning parts or debris accumulation inside the machine’s components. In addition, maintenance personnel must be provided with adequate training on how to safely operate industrial mixers as well as how to properly clean them according to industry standards.
Cleaning Protocols for Industrial Settings
When it comes to cleaning protocols for industrial settings, there are certain procedures that must be followed by all personnel involved in the process. This includes wearing appropriate protective clothing such as gloves and goggles when handling any chemicals; ensuring all machinery is switched off before any cleaning can begin; using only approved cleaners on any surfaces; conducting regular inspections of all equipment; and disposing of any waste products according to local regulations. Following these protocols will help reduce the risk of accidents occurring due to improper cleaning practices or inadequate safety measures being taken by personnel involved in the process.
Responsibilities of Employers: Providing Adequate Training and Resources
It is essential that employers take responsibility for providing adequate training and resources so their employees understand how best they can protect themselves from harm while working in hazardous environments such as when handling industrial mixers as well as other workplace hazards they may encounter on a daily basis. This includes ensuring employees receive appropriate safety training on how best they can identify potential risks before they arise; how best they can respond quickly if an accident does occur; what types of protective gear they should wear; how best they can use emergency response plans effectively; as well as how best they can use first aid kits appropriately if necessary. Without this type of information being provided by employers, employees may not have adequate knowledge about workplace safety which could put them at greater risk if something unexpected were ever happen while on-the-job site .
Labor Inspection Agencies: Regulatory Framework And Requirements
Labor inspection agencies play a critical role in ensuring workplaces are safe for employees by setting out regulations which must be followed by employing companies regarding worker safety measures such as those related specifically pertaining towards industrial mixers which must be adhered too if applicable within their jurisdiction area . This includes setting out specific requirements regarding regular inspections conducted on machines used within manufacturing plants ; identifying areas where additional protective measures need implementing ; defining standards related towards providing appropriate training programs ; defining safe operating procedures must be followed when using certain types of machinery ; establishing rules regarding reporting incidents related towards workers health & wellbeing ; outlining ways companies must handle cases involving employee injury & death caused through accidents occurred whilst under employ ; plus other various elements depending upon different jurisdictions .
Industrial Liability Laws: Claims Following Injuries Or Deaths
In some cases where an employee has been injured or killed due negligence from their employer such as not taking reasonable steps needed ensuring staff received appropriate instruction & training regarding use & maintenance involving machines used within workplace settings like those found within manufacturing plants then legal action may occur through claims made via applicable laws pertaining towards civil liability . These claims will often seek compensation for damages suffered by family members arising from loss wages , medical expenses , pain & suffering , funeral costs , plus other various legal forms relief depending upon jurisdiction . However even though employers liability coverage provides insurance protection against certain legal claims made against companys operations , there will still remain potential financial liability owed should court ruling find company liable negligence leading up incident resulting employees death whilst under employ .
Extent Of Employer Liability For Damages
The extent of employer liability for damages arising from incidents occurring under employ depends largely upon whether negligence has been considered part causing event happening . If negligence has been found then company liable paying financial compensation owed family members affected incident through court ruling ordering payment damages suffered under civil law . However even though insurance cover may exist through employers liability policy , company still remains financially liable paying out any compensation ordered via court ruling after investigation finds negligence part causing incident resulting employees death . Therefore it is essential employing companies take reasonable steps ensuring staff receive appropriate instruction & training regarding use & maintenance involving machines used within workplace settings like those found within manufacturing plants thus helping reduce potential liabilities arising out damaging events occurring under employ .
Investigations into Workplace Accidents:
When an industrial accident results in the death of a worker, an investigation is immediately launched by the Occupational Safety and Health Administration (OSHA). OSHA works to ensure that all employers are following safety protocols to protect their employees. During the investigation, OSHA will look for any violations of safety protocols or equipment issues that may have contributed to the accident. They will also seek out any witnesses to the accident and conduct interviews to get a full understanding of what happened.
In addition to determining fault, OSHA investigations also look for ways to prevent similar accidents from occurring in the future. Strategies such as improved training programs or changes in safety protocols can be implemented after an investigation. The goal is to ensure the safety of all workers in a workplace environment and prevent future tragedies from occurring.
Repercussions of Fatal Industrial Accidents:
When a fatal industrial accident occurs, there can be a number of repercussions felt both legally and socially. If negligence is determined on behalf of an employer or another individual involved in the incident, they may face criminal sanctions as dictated by law. This could include fines, jail time, or both depending on the severity of the negligence.
Beyond legal repercussions, there can also be social ones as well. Employers may find themselves under scrutiny from their employees and other businesses who are concerned about their commitment to workplace safety. There may also be public outcry for changes to safety regulations if it appears that negligence was involved in a fatal accident.
The outcomes of these tragedies can provide lessons for future prevention as well. Employers should take time to review their safety protocols and ensure they are up-to-date with current standards set by OSHA and other governing bodies. They should also review their training programs for employees and make sure that everyone is sufficiently trained on how to use equipment safely and properly before they begin working with it. Taking these steps will help create a safer work environment and reduce the chances of another fatal industrial accident occurring again in the future.
FAQ & Answers
Q: What are the dangers of working in hazardous environments?
A: Working in hazardous environments can be incredibly dangerous, with some of the most common risks being exposure to toxic materials, extreme temperatures, and dangerous machinery. In addition, workers may also be exposed to noxious fumes or combustible materials that could cause an explosion. If proper safety protocols are not followed, workers could suffer serious injury or death.
Q: What maintenance requirements must be met when cleaning mixers in industrial settings?
A: Cleaning mixers in industrial settings requires comprehensive maintenance protocols that must be strictly followed. This includes regularly checking for signs of wear and tear on the mixer’s parts and components, inspecting for potential leaks, and taking steps to ensure that all safety guards are in place before any cleaning is done. It is also important to make sure that all appropriate protective gear is worn while cleaning is taking place.
Q: What responsibilities do employers have to ensure worker safety?
A: Employers have a responsibility to provide adequate training and resources for their employees so they can safely carry out their job duties. This includes providing necessary protective equipment such as goggles, gloves, masks, etc., as well as making sure employees are aware of any potential hazards they may encounter on the job. Employers should also make sure they are addressing any risks to employee safety through regular inspections and maintenance routines.
Q: How does the regulatory framework of labor inspection agencies help monitor compliance with workplace safety standards?
A: Labor inspection agencies exist to monitor compliance with workplace safety standards by providing a regulatory framework that employers must follow. This includes making sure employers are providing adequate training to their employees on how to safely perform their duties; conducting regular inspections of workplaces; establishing health and safety regulations; and ensuring employers are meeting their obligations for providing a safe working environment for their employees.
Q: What repercussions can occur following fatal industrial accidents?
A: Following fatal industrial accidents, there can be a variety of repercussions depending on the specific circumstances involved. These include criminal sanctions against those deemed responsible for negligence if it is determined that worker safety measures were not properly adhered to; civil lawsuits brought by family members seeking damages; investigations conducted by organizations such as OSHA into the cause of the accident; and public attention highlighting the importance of workplace safety issues going forward.
The tragic death of a worker while cleaning an industrial mixer is a sobering reminder of the dangers that can exist in the workplace. Employers must ensure that they provide their employees with the proper safety training, equipment, and procedures to protect them from potential hazards. Furthermore, employers must regularly audit and inspect their facilities to ensure that safety protocols are being followed and that the necessary safety measures are in place to keep workers safe.
Author Profile
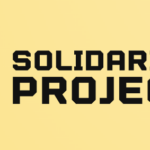
-
Solidarity Project was founded with a single aim in mind - to provide insights, information, and clarity on a wide range of topics spanning society, business, entertainment, and consumer goods. At its core, Solidarity Project is committed to promoting a culture of mutual understanding, informed decision-making, and intellectual curiosity.
We strive to offer readers an avenue to explore in-depth analysis, conduct thorough research, and seek answers to their burning questions. Whether you're searching for insights on societal trends, business practices, latest entertainment news, or product reviews, we've got you covered. Our commitment lies in providing you with reliable, comprehensive, and up-to-date information that's both transparent and easy to access.
Latest entries
- July 28, 2023Popular GamesLearn a New Language Easily With No Man’s Sky Practice Language
- July 28, 2023BlogAre You The Unique Person POF Is Looking For? Find Out Now!
- July 28, 2023BlogWhy Did ‘Fat Cats’ Rebrand and Change Their Name? – Exploring the Reasons Behind a Popular Name Change
- July 28, 2023BlogWhat is the Normal Range for an AF Correction 1 WRX?