Solving the Mystery of Endstop X Still Triggered After Retract: A Guide
The endstop for the X-Axis is still triggered after the retraction has occurred.
Endstop X Still Triggered After Retract
Endstop X Still Triggered After Retract is a common problem found in 3D printer technology. It occurs when the endstop switch at the end of the Z-axis remains triggered after the printer retracts, causing the print head to remain stationary. It can be caused by a worn or defective switch, a misaligned belt, or incorrect motors and drivers. Failed firmware updates are also known to cause this issue. This problem can be difficult to troubleshoot and may require some trial-and-error testing to narrow down the issue. Solutions can vary but often include adjusting tension on motors belts, resetting motors and drivers, and replacing faulty components. Ultimately, performing regular maintenance can help prevent this issue from happening in the first place.
Identifying & Troubleshooting Endstop X Issue
Before attempting to repair or replace any parts, it is essential to identify and troubleshoot the issue at hand. To do this, one must first check if the endstop X is indeed triggered. This can be done by observing the position of the printed parts and checking whether they are aligned correctly or not. If it appears that the endstop is not triggered, then one can attempt to investigate potential causes of the issue. This could include examining if any components are malfunctioning or if there are any obstructions blocking the axis components.
Diagnosing Mechanical Source of the Problem
Once it has been established that the endstop X is indeed triggered, one must then diagnose what could be causing this issue. To do this, one must examine in detail each component within the retract mechanism to identify which parts may have been affected by an external force or may have malfunctioned over time. In addition, one should also inspect each axis component to ensure that there are no mechanical obstructions preventing a smooth operation of the mechanism.
Repairing or Replacing Parts as Necessary
Once a diagnosis has been made as to which part(s) may need repairing or replacing, then appropriate action must be taken accordingly. This could involve repairing faulty components such as springs and screws or replacing damaged parts such as bearings and gears in order to restore functionality of the retract mechanism.
Testing Repairs & Resetting Endstop X
Once repairs or replacements have been made on the affected components, it is important to test them out before resetting endstop X back into its normal position. This can be done by running a simulation on a software program which allows for testing of repairs prior to resetting endstop X back into its original state. Additionally, once all settings have been adjusted back into its normal state, it is important to double-check that all settings have been correctly entered before continuing with further steps.
Checking Endstop X After Repair
Finally, after all repairs and adjustments have been made, it is essential to verify that endstop X is functioning properly once again. This can be done by verifying its trigger status in order to confirm if it has returned back into its correct position or not. Once confirmed that everything is back in order, then further work on other aspects of the retract mechanism can resume from here onwards.
Analyzing Settings For Solutions & Improvement
When troubleshooting the Endstop X issue, the first step is to analyze the settings of the device or software for any possible solutions or improvements. This can include evaluating software settings and commands, analyzing code for different solutions, and running tests to determine if any settings had been changed or misconfigured. It is important to take a thorough look at all of the potential causes in order to identify any potential issues that could be causing the endstop to be triggered.
Replacing Wiring & Components if Appropriate
If after analyzing the settings, it is determined that there is an issue with wiring or components, then replacing these parts may be necessary. This can involve investigating wiring issues related to endstop X, changing connectors and cables, and ensuring that all connections are secure. It is important to take into consideration any potential risks associated with replacing components in order to ensure that safety precautions are taken during this process.
Investigating Power Outages & Their Impact
Power outages can have an impact on endstops as well, so it is important to investigate any potential power supply problems that could be causing the issue. This can include checking for any irregularities in power supply levels or looking for any signs of damage or wear on power lines and cables. Analyzing the effect of outages on endstops can help identify if there are any underlying issues related to power supply that could be causing this problem.
Comparing Results with Reference Design
Once all of these steps have been taken and potential problems identified, it is important to compare current results with a reference design in order to make sure the endstop X still triggers after retracting as expected. Studying the reference design for fixes can provide insight into what adjustments may need to be made in order for the device or software to work properly again. Comparing current results with reference outputs will let users know if they need to make further changes in order for their device or software set up to function correctly again.
FAQ & Answers
Q: What should I do if my Endstop X is still triggered after retract?
A: If your Endstop X is still triggered after retract, there could be a few possible causes. First, you should check if the Endstop X is triggered and troubleshoot any possible causes. You should also diagnose the mechanical source of the problem by examining the retract mechanism in detail and inspecting all axis components. If necessary, you can repair or replace any malfunctioning parts. Once repairs are made, test them on a simulator and reset the settings back to normal. Finally, check the Endstop X again to verify that it is in its correct status.
Q: What can I do to analyze settings for solutions and improvement?
A: To analyze settings for solutions and improvement, you should evaluate software settings and commands as well as analyze code for different solutions. You may also need to investigate wiring issues related to your Endstop X by changing connectors and cables, as well as investigate potential power supply problems that could have an effect on your endstops. Comparing your results with a reference design can also help you find a solution to your issue.
Q: How do I test my repairs?
A: After making repairs, it is important to test them on a simulator in order to make sure that they are functioning correctly before resetting the settings back to normal. This will help ensure that everything is working properly before you check the Endstop X again after repairs are completed.
Q: How do I reset my Endstop X?
A: After testing repairs on a simulator in software, you will need to adjust the settings back to normal in order to reset your Endstop X. This will ensure that it is functioning properly before verifying its trigger status again.
Q: What should I do if my wiring or components needs replacing?
A: If wiring or components needs replacing, it is important to investigate any wiring issues related to your Endstop X by changing connectors and cables if necessary. Additionally, you should also investigate potential power supply problems and their impact on your endstops before comparing results with a reference design for further insight into fixing the issue.
The most likely cause of Endstop X still being triggered after retract is a mechanical issue. It is possible that the endstop switch is stuck in the “on” position or that the printer carriage has shifted and is now too close to the endstop. In either case, further investigation will be necessary to identify and resolve the underlying issue.
Author Profile
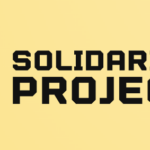
-
Solidarity Project was founded with a single aim in mind - to provide insights, information, and clarity on a wide range of topics spanning society, business, entertainment, and consumer goods. At its core, Solidarity Project is committed to promoting a culture of mutual understanding, informed decision-making, and intellectual curiosity.
We strive to offer readers an avenue to explore in-depth analysis, conduct thorough research, and seek answers to their burning questions. Whether you're searching for insights on societal trends, business practices, latest entertainment news, or product reviews, we've got you covered. Our commitment lies in providing you with reliable, comprehensive, and up-to-date information that's both transparent and easy to access.
Latest entries
- July 28, 2023Popular GamesLearn a New Language Easily With No Man’s Sky Practice Language
- July 28, 2023BlogAre You The Unique Person POF Is Looking For? Find Out Now!
- July 28, 2023BlogWhy Did ‘Fat Cats’ Rebrand and Change Their Name? – Exploring the Reasons Behind a Popular Name Change
- July 28, 2023BlogWhat is the Normal Range for an AF Correction 1 WRX?